Riser shafts feature so prominently in high rises, yet when it comes to understanding what they are and why they are needed from a fire protection perspective, there are misconceptions. There are, for example, problematic misunderstandings in relation to fire protection rules during and post-construction and the difference between intumescent paint and fire encasement.
The big issue
Riser shafts are a fundamental presence essential to building operation. Yet, in terms of their design and construction, there are two big misconceptions that need to be addressed.
The first relates to the differences between fire protection rules and codes of practice during construction (i.e., HSG 168 and the Joint Codes of Practice) and regulations post-construction. Approved Document B of the Building Regulations covers fire safety matters within and around buildings. Both need to be adhered to, but the former is little understood and generally ignored.
In order to assure safety, the design of the riser shaft has to be undertaken meticulously in accordance with Approved Document B. The riser shaft is typically encapsulated within a two-hour fire wall around it. The doors into that shaft need to offer one-hour protection. The shaft itself can vertically be any number of floors from 2-50; the design standards don’t specify any details regarding temporary protection required during construction. It would need to be horizontally fire protected where it goes into different fire compartmentations, which may be at basement level 1 or the 50th floor into the plant room. The horizontal fire protection must be supported off of materials which are Class A2 or better.
Wherever the fire compartmentations are there would need to be two-hour horizontal fire protection, i.e., a floor of 2-hour fire resistance. At this stage, it is the architect’s responsibility to design to these standards so that fire safety is not compromised when the building is handed over.
During construction however, there is a completely different set of rules. As the designers and main contractors have to design details that prevent the passage of smoke and flame from one floor to the other, there should be temporary fire doors installed on each level, and every 10 floors there needs to be half an hour horizontal fire protection.
As an example, this is where RiserSafe® a system which forms and seals the riser shaft in one action, preventing the passage of smoke and flame on every floor as well as offering 90 minutes fire integrity on each floor.
But there is a contradiction. In the first case, you may potentially have a 50-storey open shaft with two hours’ fire compartmentation at the top and bottom of a structure. Yet, during construction, at every tenth floor there has to be half an hour fire protection.
The two do not add up and it is resulting in a great deal of confusion. Both are required yet neither complement each other.
The second coming
The next issue is the failure to understand the difference between intumescent paint on steel and the encasement of steel beams. Steelwork will be specified typically as having two-hour fire resistance. This is achieved by putting intumescent paint on the steel which expands in the event of fire. When this occurs, it creates a form of insulation against the steel to prevent it reaching above 550 degrees over two hours and softening causing structural failure.
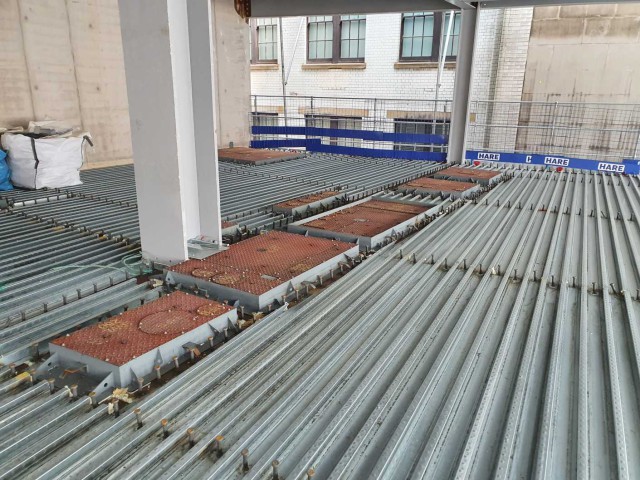
Now, it is important to remember that a two-hour fire compartment is different. The wall or the two-hour floor has to be tested in two ways: integrity and insulation. In terms of integrity, if it is in a furnace of 1000 degrees for over two hours, does it stand up? Or is it compromised? When it comes to insulation, the 1000 degrees heat cannot transfer more than 140 degrees to the other side of the compartment. The problem is that 140 degrees isn’t quite 550 degrees. The two are vastly different.
What happens is that in a riser of a steel frame building, there are steel beams at every floor level with the wall finish below the steel. So, the intumescently coated steel is sandwiched between the two compartments (riser and office compartment typically). There is a misconception here that the two-hour protection on the steel is the same as the two-hour protection required for the wall. But it isn’t, because 550 degrees is passing into the compartment when only 140 degrees is permitted.
To overcome this issue, the steel has to be encased. However, the problem here is that at the moment there isn’t sufficient attention paid to the size of the fire encasement. This has a knock-on effect on the riser and the space available for M&E services. The real concern is that it creates incredibly difficult details which have to be remedied onsite at a huge cost, with M&E models having to be re-designed and fire encasement details being added to the drylining package.
Therefore, more attention needs to be paid on including this on the drawings and in the models so the encasement can go into the M&E modelling. In extreme cases, not taking the size of the encasement into consideration can reduce the riser’s size by 30%.
What can be done?
Each of the issues that have been raised can cause massive problems onsite, and the best way to overcome them is through better education. Main contractors – which are increasingly becoming key stakeholders – need to be brought up to speed about the different fire compartments. Designers on the other hand need to have an understanding of the temporary site rules, as at the moment their designs are not translating as effectively as they should.
Finally, there must be better education on understanding the difference between intumescent coatings and fire encasement. Many construction professionals are under the misleading impression that the two are interchangeable when in fact they are entirely different.
Education must come from the top to be filtered down to everyone. With the building safety regulator coming onboard things have to get better, particularly in terms of fire safety. Whilst the likes of technology can certainly play a part in visualising what is right to highlight the wrongs, education is something which comes earlier in this process, meaning it is more likely to make an impact. We can’t keep moving in the current direction we’re heading in – we must change course and utilise education to combat the misconceptions relating to the riser shaft. Afterall, it does have an impact on everyone working on a construction project.
SOURCE - https://modbs.co.uk/news/fullstory.php/aid/19704/Education_at_the_core_of_demystifying_Riser_misconceptions_.html